JORGE GUTIERREZ HUEZO
Jorge Gutierrez's Portfolio
Projects

1. Presso Vent Cover Design
Redesign the steam vent covers used in the Presso Machine improving its performance
2. Presso Balloons' Testbed
Built a testbed to test the reliability of the balloons used in the Presso Machine
3. Mars Robotic Grip and Energy Analysis
Design and built an energy efficient robotic grip that could be used in Mars.
4. Formula 1 Car Design Project and Analysis
Designed a Formula 1 Car in Siemens NX
5. Creative Decisions and Design Robot Competition
Built a robot for the Design Robot Competition and won
Presso Vent Cover Design
The original vent covers used in the Presso machine were breaking when the users released the clips used to stretch the garments. As the clip went back to its original position it hit the vent covers, breaking them. In addition, Presso had 3 different vent cover designs for 5 different machines.
To solve this issue, I designed a new version of the vent cover. This version was strong enough to withstand the impacts from the clips and could be used in all of the machines.
The top picture shows the final design and the bottom one shows the final 8 designs.
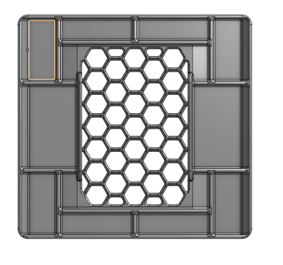

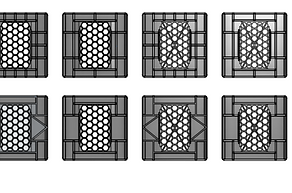
Presso Balloons' Testbed
Original Testbed Design

As expected, the first prototype deviated from the original design shown above. The four main subsystems of the testbed are the enclosures, the steam, the dryer systems, and the electrical system shown below.
Building the prototype was a challenge because I only had available the tools at the workshop, and therefore, most of the testbed had to be manufactured using handheld tools.
Electrical Subsystem
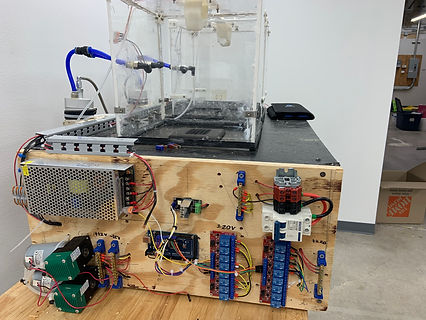
At Presso, I was assigned to design and manufacture a testbed that aimed to determine the lifespan of the balloons used in the Presso Machine.
The balloons were used by the machine to stretch the shoulder area of a long sleeve shirt. These were made of silicone and were prone to failure.
Testbed Final Assembly
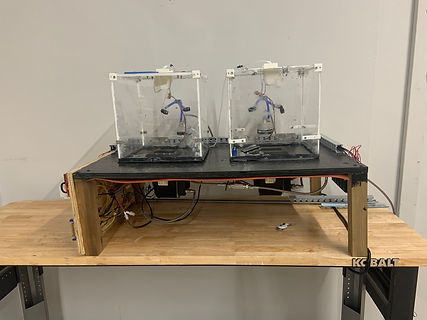
Overall, I was successful and learned a lot from this challenge. The most valuable lesson was that designing for assembly is imperative when doing a project. In order to save money for the company I decided to avoid prefabricated parts. This saved money on the short run, but I could have saved time an effort if I had done this differently.
Mars Robotic Grip and Energy Analysis
Mars Retrieval Lander

For our Capstone Design class at Georgia Tech, the team and I decided to do a self-sponsor project regarding the Mars Exploration Program and the 2028 Sample Return Mission. At first, the team wanted to build a fully functional rover but due to the time constraint the scope of the class the team decided that designing an energy efficient robotic gripper was going to be more useful for the 2028 Sample Return Mission.
The new design we came up with was an adaptation of a Robotiq 2F-85 robotic gripper. We decided this was the best course of action because designing a robotic gripper from scratch was counterproductive as there are many options on the market and re-inventing the wheel is not necessary. For our design we redesigned the tips of the Robotiq gripper improve its hold on the sample tube. We also added a new rubber piece at the palm of the gripper. This piece allows our design to carry and store two sample tubes in one movement.
Our Gripper Design
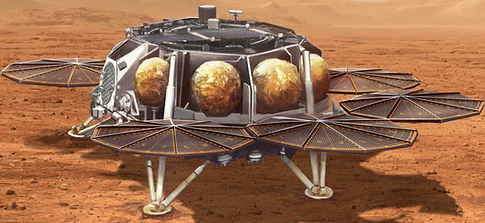
Final Assembly
By retrieving two sample tubes instead of one, our robotic gripper would save about half of the energy previously required and would decrease the mission time from 42 days to 21. This project is still in the prototyping face and further testing is required to collect the data to determine exactly how much time and energy is saved.
Creative Decisions and Design Robot Competition
Final Robot and Champion

Subsystems
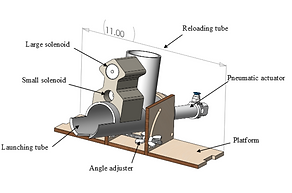

For this class, our team designed a robot that had to accomplished two tasks and an optional task for extra points. These tasks were to score two ping-pong balls into a hexagon area built out of solo cups by throwing them and to score another two ping-pong balls into another hexagon area by any means. The optional task was to grab a money ball placed in the arena and score it in the second hexagon arena. The team successfully built a robot with a set of catapults used to accomplish the first task and a pneumatic actuator canon used to grab the money ball and score the three balls accomplishing the second and third tasks. The team won the final competition by outscoring 40+ teams.